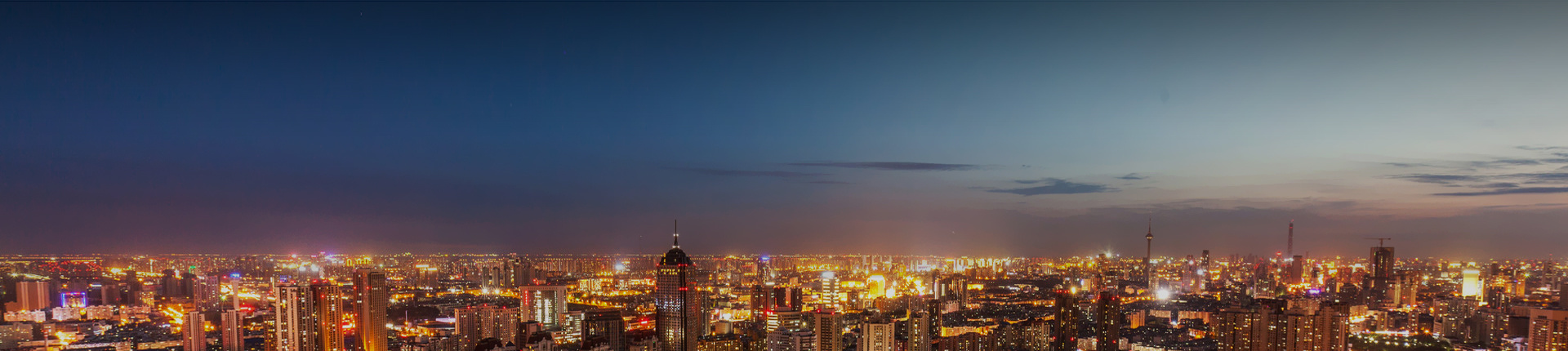
24
2021
/
06
24
2021
/
06
24
2021
/
06
24
2021
/
06
Yi Xing Hongda Universal Facility Co., Ltd.

Address:No. 32, Chuanbu Road, Dingshu Town, Yixing City, Jiangsu Province (in Taodu Industrial Park)

E-mail:yxhd@yixinghd.com
Copyright © 2022 Yi Xing Hongda Universal Facility Co., Ltd. 苏ICP备18041159号-1 www.300.cn SEO